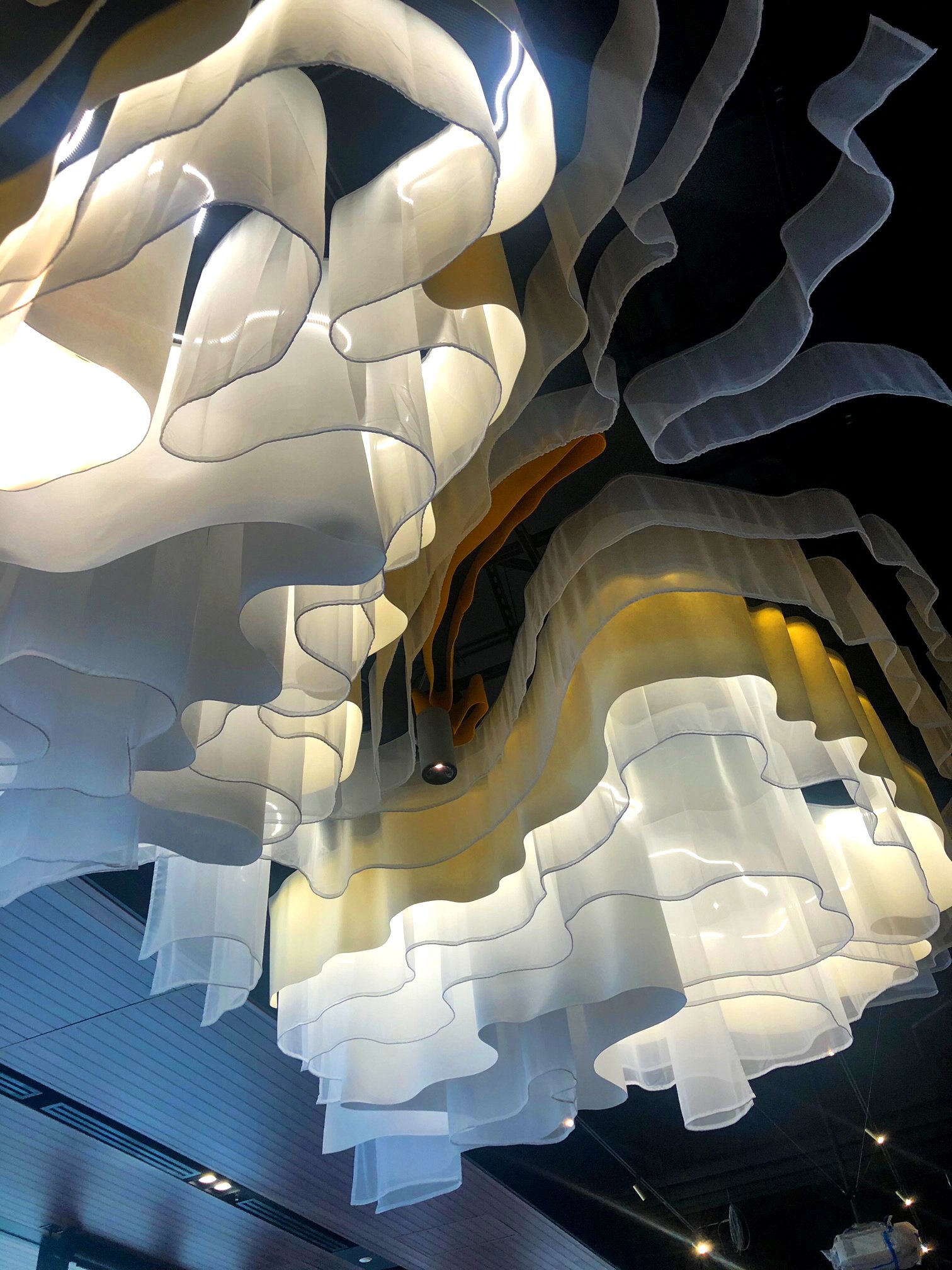
Our Capabilities
Design and Fabrication
Two sides of the same coin. Both need to be in sync for success. It might sound easy, but it takes a lot of effort to pull this off. That’s why we’ve divided ourselves into battalions of specialists, each with its own skilled leader. We’re planning to take over Canada one day, but for now… we make cool stuff!
-
1. To create, plan, problem solve, innovate, etc.; To put one’s ideas into tangible form. 2. To build a physical or digital manifestation of the imagination. 3. To delve into the depths of your subconscious and imagine the unimaginable, using everything that is in your box to dream something that is outside of all boxes; drafting, drawing, sketching, reviewing, redrawing, rereviewing and polishing to perfection that which can be fabricated beautifully.
Pencils down! -
1. To make, construct, etc.; manufacture 2. To invent. 3. To take everything you have ever learned and a pile of materials from every corner of the periodic table, and weld, pound, screw, glue, sew, tie, wire and fiberglass them all together into a shape that looks nothing like any of the individual elements, slap on a coat of paint and several thousand stamps, get your picture taken standing next to it glowing with pride, and push it out the door.
Order up!
Wood
When a package of drawings hits the table in the wood shop, or a set of parts comes to the floor from our in-house CNC router, our highly skilled woodworkers must determine the best method of construction. This often requires both creative thinking and experience in build sequencing. Whether working in exotic woods like bamboo, teak or tigerwood to create museum quality case work, or dimensional lumber and the various species of plywood and bender board used in more basic construction, efficiency and precision are always at the top of the decision-making process.
After the critical thinking and planning stage are complete, the dust begins to fly, and the saws begin to sing! The sound of ripping, planing, sanding and routing fills the shop as the various components of the job begin to take shape. Next, any variety of joinery might be employed, from tongue and groove and biscuit joining, to brads and screws and glued pressure fitting. A finished piece might be covered with a veneer of figured maple or cherry or be sanded to a smooth surface to receive a paint finish. Whatever the case, our wood shop consistently turns out a sturdy, beautifully crafted product that not only serves its role in the job as a whole, but also represents our commitment to superior fabrication.
Once that’s done, we start sweeping up.
-
Table, band, panel, chop & miter saws
Drill Press
Pneumatic nailers and staplers
Disc and belt sanders
Oversized belt sander
Time-saver sander
Sandblast booth
Multicam CNC router with 5’ x 10’ bed -
Plastic
Glass
Fiberglass
Vinyl
Laminate
Good old-fashioned wood, nails and glue
Metal
Our team of artisan metal workers can bend, cut, join and roll all manner of steel and aluminum into whatever shape or contortion a job requires. They are chilly on the cold saw, masters at the mill and whether it be tig, mig or just plain big, they take real pride in the high standard applied to each and every weld. Oh, and did we mention they are WABO certified?
You may not always see their work in the finished product, but rest assured, each piece of rolled pipe or plasma cut stainless steel has been lovingly executed, each angle checked with an exacting eye and each hole drilled and tapped straight and true. They can make you a thirty foot tall rocket or a gracefully whimsical flower and everything in between…just don’t let them make you a sandwich without washing their hands first!
-
CNC Mill
Tube bender
Bridgeport Precision Tool
TIG and MIG Welders
Plasma cutter
Variety of metal saws and drills
Metal Lathe
Pemserter
Coping Machine -
Stainless steel
Aluminum
Steel
Brass
Bronze
Copper
Paint
Due to the wide variety of materials we use, like steel, plastic, urethane, polycarbonate, acrylic and sometimes even wood, (just to name a few) our paint shop personnel need to have a deep understanding of the complex chemistry involved in getting the paint to stick…and stay stuck! We engage in near constant research and development and work with materials experts within the industry to always ensure a safe, vibrant and durable paint finish. This involves taking the environmental factors that the paint might be exposed to into careful consideration. Will there be extreme heat or cold? Will the paint be under water or near live animals?
In designing a paint finish, our painters chose a medium. Should it be latex or acrylic? Polyester or urethane? They then work closely with the client representative to produce a series of samples that will determine everything from color intensity and fade, to texture and contrast as well as which techniques might be employed, be it airbrushing and washes, or hand lettering and pin striping.
But that’s not all! Because a paint finish might also incorporate things that are not, in fact, paint. Like vinyl graphics or fabric dying and aging, or even glitter. (Don’t forget the glitter!)
Once signed off on by the client, our painters can be counted on to scrutinize every glossy surface and take great care to make sure the faux bark or rocks look utterly convincing, even in natural daylight. Ultimately, theirs is the final stop in making our work shine.
Unless, of course, it’s a matte finish. Then it’s not supposed to shine.
-
40′ x 16′ x 18′ industrial spray booth
Bench spray booth
Spray guns (high-volume, low pressure)
Fresh air supply system
Matthew’s Paint Intermix System -
Latex paint
Two-part component paints
Automotive finishes
UV clear coat
Gold and various metal leafing
Luminor / Make It Metal capabilities
Textured surfaces
Faux finishes
Sculpt
From teeny tiny to, “Wow, that’s big!” In the sculpt shop, the parameters of the things we create can vary wildly from one project to the next. Depending on factors like scale, the number and complexity of the component parts and the final material a sculpture is to be cast in, we might decide to go “old school” or “new school” or a combination of both.
We start with either an in-house or client-supplied design. Then we create a small-scale model, or maquette. By using this miniature to zero in on the final details and design choices, we’re able to avoid making costly changes to the full-scale piece once it’s begun. The same basic idea is used to streamline the design process when sculpt is called upon to create architectural white models that help in determining how an installation will work within a specific space.
Old school.
People are often surprised to learn that Dillon Works still creates a lot of our sculptures in much the same way that artists did hundreds of years ago. With a keen eye for detail and a solid working knowledge of anatomy, characterization and an ever-changing spectrum of design aesthetics, it is often just the artist and his tools that find the finished sculpture within the clay or block of foam.
New school.
In other instances, we might utilize the latest in modern technologies…things like laser scanning, 3D printing or CNC three-axis routers. These new state- of-the-art tools allow us to render large or small components in a fast, efficient manner that saves us the trouble of building every form from scratch.
From there, any variety of tools and techniques might be used to get to the finished product. Everything from our giant foam lathe and custom fabricated sculpting tools, to hot wire and urethane spray systems. Whether it be bronze insects or a thirty-foot tall creature from another dimension, the sculpt department is always up to the challenge is creating visually striking works that delight and entertain at any scale.
-
Foam lathe
Metal mill/drill
3D printers
Various sculpting and carving tools -
Foam
Wood
Clay
Plastic
Epoxy
Mold
You just have to be able to think upside down and backwards, which sounds complicated but it’s really not. Most of what we do in the mold and casting department involves creating a brand new “part” out of a combination of chemical reactions, artistic technique and mechanical technologies.
First, we create a mold out of a variety of materials…plaster, urethane, fiberglass, epoxy or silicone just to name a few. Then we choose a suitable casting material by asking a series of important questions. Will the part be clear or tinted? Does it need to be hard enough to sand or soft enough to flex? Will it allow for proper adhesion for the paint finish?
Once those questions have been answered, we ask some more.
Will the mold be used to hand laminate the part or will it receive a spray-coating or injection? Can the part be roto-cast? Which variation of pressure, vacuum, motion or temperature will be used in the casting process? And how many times can the mold be used before it begins to fail?
At this point, the challenge becomes one of consistency. Acceptable parts need to be uniform and free of flaws and air bubbles. Even though every drop of material that goes into a mold is measured to the gram and temperatures carefully monitored, parts have way of coming out differently. Constant vigilance and concentration are required by our team to ensure that each piece comes out as well as we can make it. In the mold and casting department, we care a great deal about making a good impression.
You see what we did there? Impression? Mold and casting.
-
Vacuum-form machine
Vacuum chamber
Pressure chamber
Curing ovens
Roto casting machine
Meter mix machine -
Silicone rubber
Fiberglass
Urethane foam
Vinyl ester resin
Plaster
Latex rubber
Polyester resin
Polyurethane resin
Plastic
To be successful in the outcome of any job it is essential to choose the right materials for construction. Many times, environmental factors like weather exposure, public accessibility and durability come into play. While wood and steel both have their place, sometimes steel is just too heavy, and wood doesn’t get along well with water. Both are hard to see through.
Enter plastics!
“Plastics” of course, is a broad term that refers to any number of different products, brands and material properties. They can be clear or opaque, hard or flexible, heavy or lightweight. By their very nature, plastics are malleable and can be routed, laser-cut, vacuumed-formed and even extruded. Understanding all the variations and uses of plastics is a discipline unto itself. For instance, if you ask one of our fabricators about working with plastics, you might get something like this:
“Well, if you’re looking for a decent clear with a good fire-rating that doesn’t crack, has a high heat deflection and can take a direct printing, you’re looking at polycarbonate. Or maybe you want something you can polish so it gleams like glass? That’d be your acrylic. What about a low melting point, low water absorption? That’s PETG, real nice for vacuum-forming. Maybe it’s got to be tough? Well, then we’re talking PVC, very dense, great for signage or solid structures. Need something to slide? Like a window or interactive component? UHMW’s got you covered, low friction.”
Don’t even get them started on high pressure laminates or custom decorative sheeting. Anyway…I think you get the picture.
3-D Printing
3-D printing is a method of additive manufacturing that uses small beads of resin or other filament to build up layers that will form a part or component. With varying build envelopes, our 3-D printers are an excellent tool for rapid prototyping, testing design concepts in real space or incorporation into the final project.
Beginning with a virtual model built with the aid of a computer and design software such as Rhino, SOLIDWORKS or AutoCAD, our operator must determine the best method for printing…whether supports will be needed or if the part can be rendered in halves and put together later.
Unlike a copy machine, Fuse Deposition Modeling must take things like structural supports and gravity into account. For this reason, we often incorporate tabs into the printing process which are removed after the part is completed.
CNC
Unlike 3-D printing, which is an “additive” form of rapid-prototyping, CNC, or Computer Numerical Control, is a “subtractive” form of manufacturing. We place materials such as wood, plastic or foam on the five-by-ten-foot bed which are held there by a powerful vacuum underneath. A series of eight interchangeable cutting bits are switched out automatically as the patterns are separated from the source material. Before any of this can happen however, our CNC operator, again working from “cut files” created by our design team, must determine the appropriate bit size, tool path and feed rate the machine should follow. That information is then entered into the CNC machine’s dedicated computer and the program is initiated.
Digital
In the over thirty-five history of Dillon Works we’ve seen many technological developments within the industry, many of them digital in nature. From design software like AutoCAD to table saws that stop in the millisecond your finger gets too close to the blade, there have been any number of truly amazing innovations. Perhaps none have been as dramatic as the ones that have occurred with new tools in lighting and electronics.
With the widespread introduction of LEDs a whole array of possibilities has opened up. Easy to wire and requiring less power, these small, low voltage, but incredibly bright and long-lasting lights give considerably more bang for the buck than their incandescent predecessors. In addition to standard DMX controllers and RGB color-mixing effects, there are now several exciting new products on the market that expand our designers’ palette even further. One example of this is a semi-flexible panel material that is covered in thousands of tiny LED lights—easily cut and shaped as needed, this versatile material eliminates hot spots common with halogen and fluorescent lighting while saving hours and hours of wiring time. Another is the IMS (Integrated Media Server). This handy device is a state-of-the-art show control system that can run multiple programs of video, audio, lighting and mechanical effects to a preprogrammed time code.
These tools bolster our creative team’s tool box as they set about designing and building the dramatic retail spaces, play areas and show stopping displays that our clients have come to expect.
Effects
Yep. We’ve got a few tricks up our sleeves.
When the company motto is “Design and fabrication of almost anything…” you kind of need to be prepared for anything. For instance, if a client says they want a giant bowl of clam chowder, they’re going to want to see it “steam.” If they want a sixteen-foot-tall waterfall or an enormous bowl of leaping flames…inside a busy convention center, we do our best to try and make it happen. What about a police car… twisted and smoking on a public sidewalk? Or a set of massive spinning snowflakes…or your company mascot winking and waving at satisfied customers as they drive away from your place of business? Talking trains, water features…we do all that. Because we love a creative challenge and adding that extra something special that really makes your project stand out!
So, go ahead. Ask.
We’re listening.